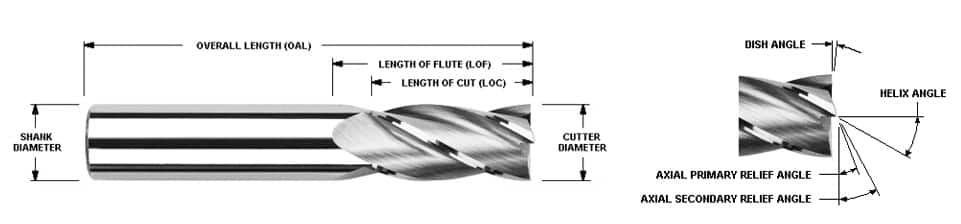
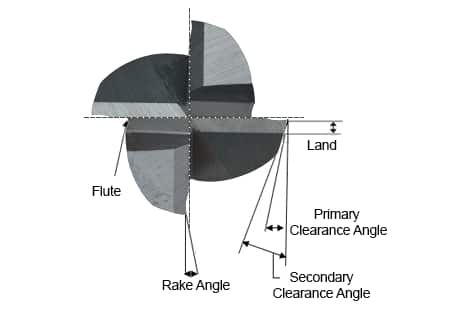
Essential Summary:
For fast cuts and the greatest rigidity, use shorter end mills with larger diameters
Variable helix end mills reduce chatter and vibration
Use cobalt, PM/Plus and carbide on harder materials and high production applications
Apply coatings for higher feeds, speeds and tool life
End Mill Types:
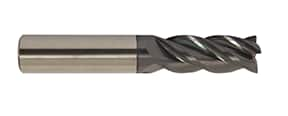
Square end mills are used for general milling applications including slotting, profiling and plunge cutting.
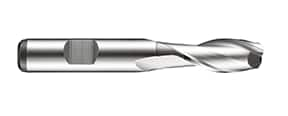
Keyway end mills are manufactured with undersized cutting diameters to produce a tight fit between the keyway slot they cut and the woodruff key or keystock.
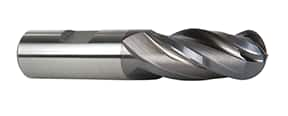
Ball end mills, also known as ball nose end mills, are used for milling contoured surfaces, slotting and pocketing. A ball end mill is constructed of a round cutting edge and used in the machining of dies and molds.
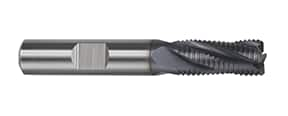
Roughing end mills, also known as hog mills, are used to quickly remove large amounts of material during heavier operations. The tooth design allows for little to no vibration, but leaves a rougher finish.
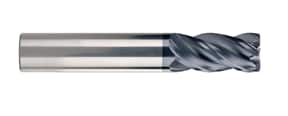
Corner radius end mills have a rounded cutting edge and are used where a specific radius size is required. Corner chamfer end mills have an angled cutting edge and are used where a specific radius size is not required. Both types provide longer tool life than square end mills.
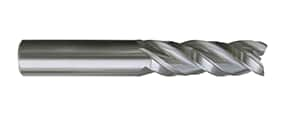
Roughing and finishing end mills are used in a variety of milling applications. They remove heavy material while providing a smooth finish in a single pass.

Corner rounding end mills are used for milling rounded edges. They have ground cutting tips that strengthen the end of the tool and reduce edge chipping.
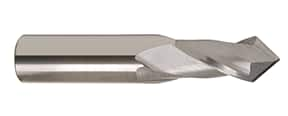
Drill mills are multifunctional tools used for spotting, drilling, countersinking, chamfering and a variety of milling operations.
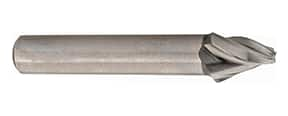
Tapered end mills are designed with a cutting edge that tapers at the end. They are used in several die and mold applications.
Flute Types:
Flutes feature grooves or valleys that are cut into the body of the tool. A higher number of flutes increases the strength of the tool and reduces space or chip flow. End mills with less flutes on the cutting edge will have more chip space, while end mills with more flutes will be able to be used on harder cutting materials.

Single Flute designs are used for high-speed machining and high-volume material removal.

Four/Multiple Flute designs allow for faster feed rates, but due to the reduced flute space, chip removal may be a problem. They produce a much finer finish than two and three flute tools. Ideal for peripheral and finish milling.

Two Flute designs have the most amount of flute space. They allow for more chip carrying capacity and are used primarily in slotting and pocketing nonferrous materials.

Three Flute designs have the same flute space as two flutes, but also have a larger cross-section for greater strength. They are used for pocketing and slotting ferrous and nonferrous materials.
Cutting Tool Materials:
High Speed Steel (HSS) provides good wear resistance and costs less than cobalt or carbide end mills. HSS is used for general-purpose milling of both ferrous and nonferrous materials.
Vanadium High Speed Steel (HSSE) is made of high speed steel, carbon, vanadium carbide and other alloys designed to increase abrasive wear resistance and toughness. It is commonly used for general applications on stainless steels and high silicon aluminums.
Cobalt (M-42: 8% Cobalt): Provides better wear resistance, higher hot hardness and toughness than high speed steel (HSS). There is very little chipping or microchipping under severe cutting conditions, allowing the tool to run 10% faster than HSS, resulting in excellent metal removal rates and good finishes. It is a cost-effective material ideal for machining cast iron, steel and titanium alloys.
Powdered Metal (PM) is tougher and more cost effective than solid carbide. It is tougher and less prone to breakage. PM performs well in materials < 30RC and is used in high-shock and high-stock applications such as roughing.
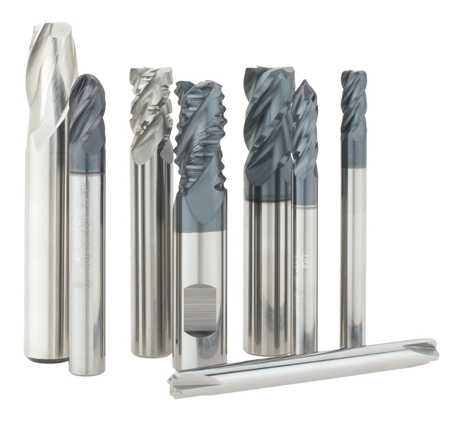
Solid Carbide provides better rigidity than high-speed steel (HSS). It is extremely heat resistant and used for high speed applications on cast iron, nonferrous materials, plastics and other tough-to-machine materials. Carbide end mills provide better rigidity and can be run 2-3X faster than HSS. However, heavy feed rates are more suitable for HSS and cobalt tools.
Carbide-Tips are brazed to the cutting edge of steel tool bodies. They cut faster than high speed steel and are commonly used on ferrous and nonferrous materials including cast iron, steel and steel alloys. Carbide-tipped tools are a cost-effective option for larger diameter tools.
Polycrystalline Diamond (PCD) is a shock- and wear-resistant synthetic diamond that allows for cutting at high speeds on nonferrous materials, plastics, and extremely difficult-to-machine alloys.
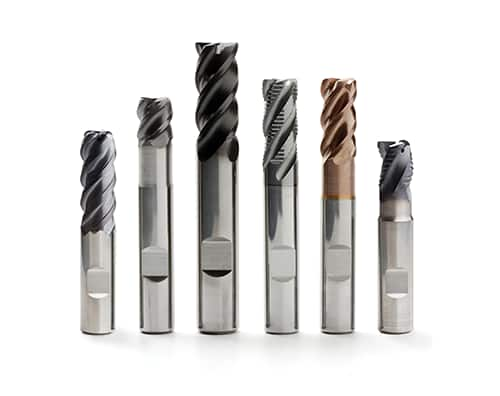
Standard Coatings/Finishes:
Titanium Nitride (TiN) is a general-purpose coating that provides high lubricity and increases chip flow in softer materials. The heat and hardness resistance allows the tool to run at higher speeds of 25% to 30% in machining speeds vs. uncoated tools.
Titanium Carbonitride (TiCN) is harder and more wear resistant than Titanium Nitride (TiN). It is commonly used on stainless steel, cast iron and aluminum alloys. TiCN can provide the ability to run applications at higher spindle speeds. Use caution on nonferrous materials because of a tendency to gall. Requires an increase of 75-100% in machining speeds vs. uncoated tools.
Titanium Aluminum Nitride (TiAlN) has a higher hardness and oxidation temperature versus Titanium Nitride (TiN) and Titanium Carbonitride (TiCN). Ideal for stainless steel, high alloy carbon steels, nickel-based high-temperature alloys and titanium alloys. Use caution in nonferrous material because of a tendency to gall. Requires an increase of 75% to 100% in machining speeds vs. uncoated tools.
Aluminum Titanium Nitride (AlTiN) is one of the most abrasive-resistant and hardest coatings. It is commonly used for machining aircraft and aerospace materials, nickel alloy, stainless steel, titanium, cast iron and carbon steel.
Zirconium Nitride (ZrN) is similar to Titanium Nitride (TiN ), but has a higher oxidation temperature and resists sticking and prevents edge build up. It is commonly used on nonferrous materials including aluminum, brass, copper and titanium.
Uncoated tools do not feature supportive treatments on the cutting edge. They are used at reduced speeds for general applications on nonferrous metals.
Post time: Nov-26-2020